We supply Liquefied Petroleum Gas (LPG) Cylinders and Bottles of various sizes and capacities.
Liquid Petroleum Gas (LPG) Bottling Plants
We Undertake Turnkey Contract For Bulk Installation Of Lpg Bottling Plants For Filling Lpg Cylinders. These Are Sophiticated Plants With Or Without Carousel. We Also Provide Special Instrumentation For Complete Automation To Enable Faster And Accurate Cylinder Filling. Bottling plant is a plant where beverages are put into bottles with a cap. These bottles are widely used for storage purposes. Liquefied petroleum gas (LPG) consists mainly of propane, propylene, butane, and butylene in various mixtures. However, in the United States, the mixture is mainly propane. It is produced as a by-product of natural gas processing and petroleum refining. The components of LPG are gases at normal temperatures and pressures.
LPG bottling plant is a plant where LPG is put into bottles for storage. The plant has the facility to recieve bulk LPG by pipeline from a reliable source or any area. This is the safest and the cheapest way of transporting bulk LPG.
The plant is equipped with hydraulic cylinder testing equipment for periodic testing of the cylinders. To ensure safe and accurate filling of the cylinders well experienced technical people should only be employed in the working of the plant.
Tips While Working With LPG Bottling Plant. The filling machines should be provided with pneumatic cut off system to automatically cut off the LPG supply when the cylinder is filled. The filling pressure should not exceed design pressure of the liquid. Cylinders have a standard weight and all cylinders should be checked for their weight after they are filled.
The compact valve tester should be calibrated to detect leakage from the cylinder.Defective cylinders should be evacuated and evacuation should be done either through one or two vessels. From these vessels LPG is transferred to the storage vessels through a pump.Security caps should be provided while performing any test with LPG. The sequence of operation should be strictly followed. To avoid undue accumulation the cylinders should be immediately shifted to storage after filling. The bottling plant has its own system of stringent safety and quality control checks built-in at different stages.
The quality control checks at the bottling plants are carried out at 3 stages:spurious cylinders, cylinders with missing O-Rings and cylinders due for pressure testing. Post-filling Quality Control Checks - In the post-filling checks, it is ensured that all the cylinders filled on the automatic cut-off weighing scale / filling machines are subjected to 100% cross - checks for weight. Statistical Quality Control Checks - These checks include all pre-filling and post-filling Checks in addition to checking the quality of the seal.
- • 3kg and 5kg LPG Cylinders
- • 6 kg and 12 kg LPG Cylinder
- • 15kg and 48kg LP Gas Bottles
- • Other capacities LPG Bottles
- • All types of LPG Containers
- • Small LPG Domestic Cylinders
- • Domestic LPG Bottle
Technical Specification
Design Pressure | 17.16 to 22 Bar |
---|---|
Design Temperature | 10 Deg C to + 65 Deg C |
Design Code | ASME, PD 5500, AD Merkblatter and others |
Volume | ( 3 | 5 | 6 | 9 | 12 | 15 | 19 | 48 ) kgs |
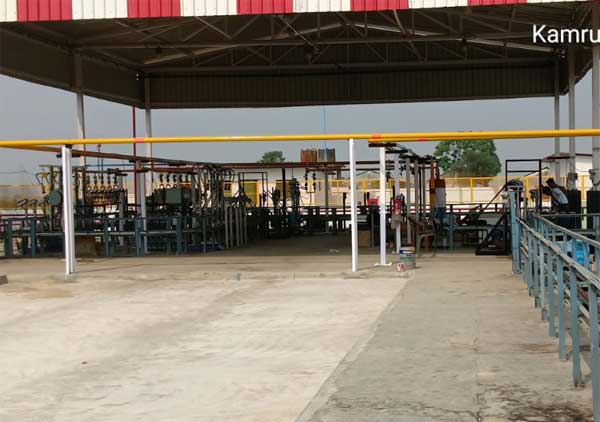
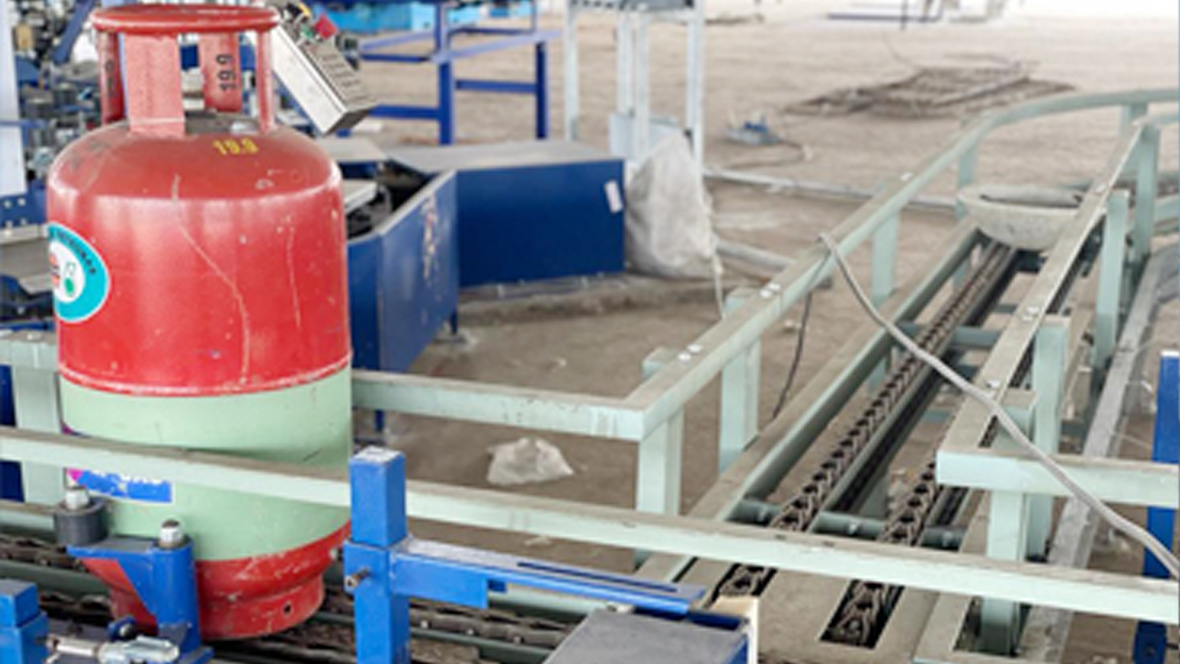